Access to world-class microfabrication technologies has enabled a team of Monash University researchers to develop an affordable and scalable production method for low temperature and high-performance perovskite solar cells.
Exploiting the capabilities of a microfluidic device, Dr Adam Surmiak and Dr Monika Michalska and their collaborators from the Department of Chemical and Biological Engineering and the Department of Material Engineering at Monash University have created of one of the highest performing, low-temperature, perovskite solar cells (PSCs) in the world.
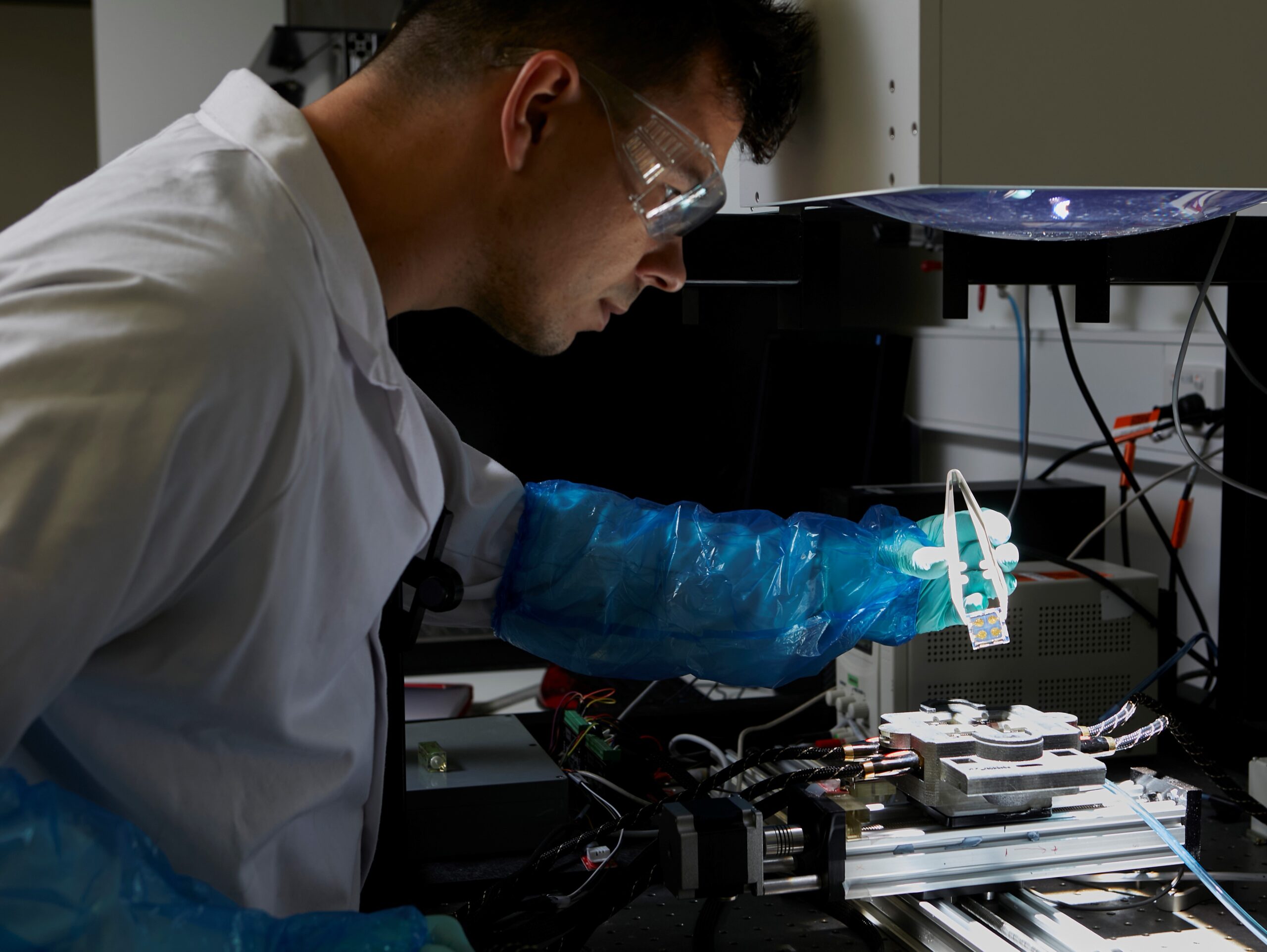
Perovskite is an ideal material for creating solar cells, as it is lightweight, cheaper to produce at scale and as efficient as today’s leading photovoltaic material, silicon. Importantly, perovskite materials can be easily deposited from a solution onto the fabrication surface and even applied on flexible substrates while maintaining their high performance. For example, polyethylene teraphthalate (PET) is used as the plastic substrate for the solution-based deposition process that creates the perovskite thin film layer. PET is a transparent and low-cost polymer, but the material has a relatively low upper processing temperature limit (150 oC). While perovskite thin films can easily be fabricated under these conditions, the other layers in a PSC are usually produced by high temperature processes that can melt plastics such as PET.
In a PSC, the light-absorbing perovskite is sandwiched between two thin films of charge-transporting material. These functional layers play an intrinsic role in the photovoltaic performance of a PSC, influencing its power conversion efficiency, long-term stability, and scalability. Dr Surmiak’s microfluidic device enables fabricators to apply inexpensive techniques and simple approaches to depositing these additional PSC layers. His microfluidic strategy effectively eliminates the need for the high temperature process treatments used in traditional PSC recipes.
The mixing capabilities of the microfluidic device were used to facilitate nickel oxide (NiO) nanoparticle deposition. Thanks to this device developed by Dr Surmiak, the team could make a uniform, low-temperature NiO thin film layer, which functions as the hole-transporting layer (HTL) of a PSC.
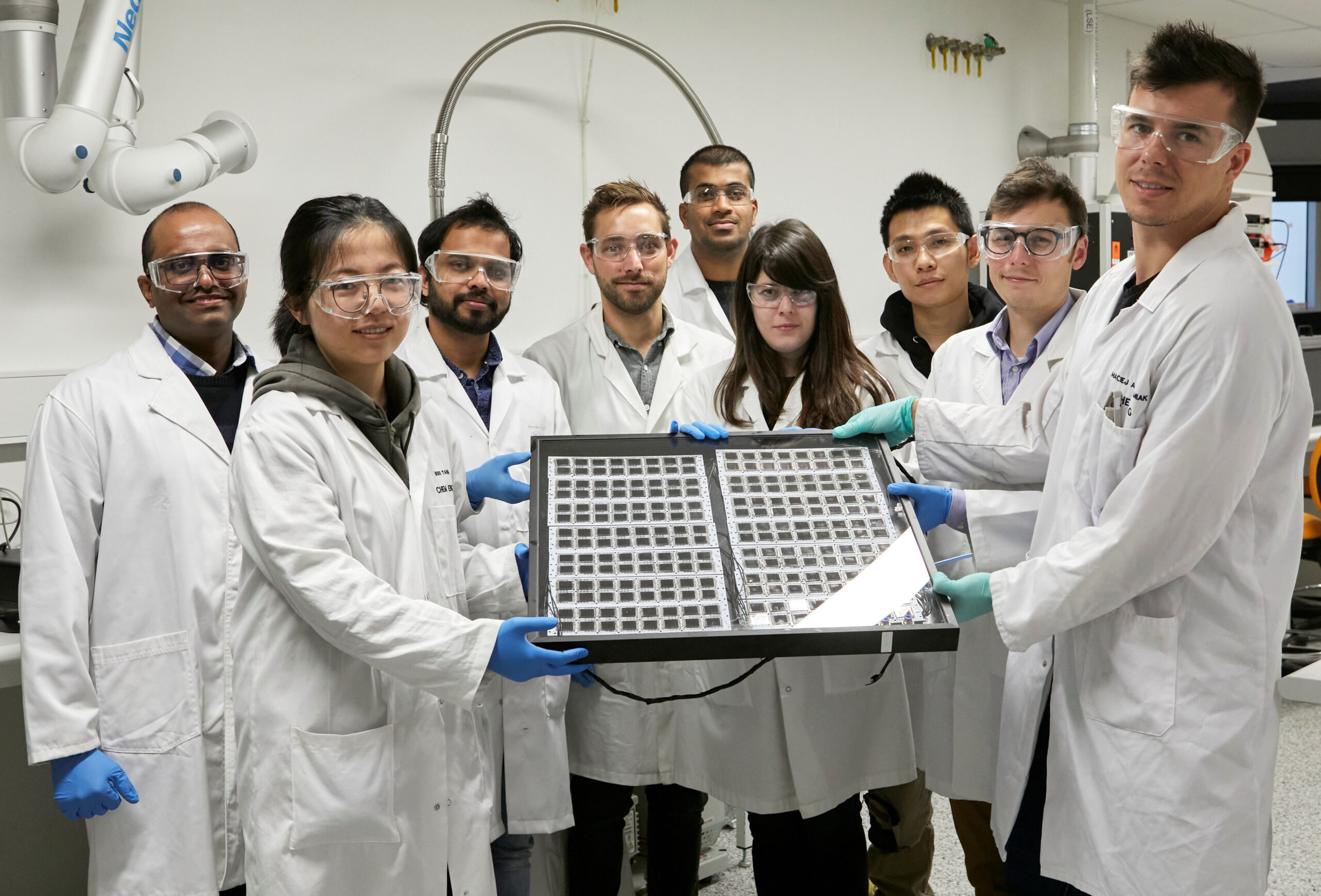
The inspiration to integrate microfluidics into the fabrication of PSCs occurred to Dr Surmiak while attending ANFF-SA’s Microengineering School. This annual program provides Australia’s brightest engineering students with an insightful introduction to the design and fabrication of microfluidic/ electronic, MEMS, optical and sensing chips with hands-on practical experiences in world-class cleanroom facilities.
The program sparked a productive collaboration, initially between Dr Surmiak and ANFF-SA, resulting in improved flow simulations and the development of his mixing device to optimise the NiO nanoparticle dispersion. As word spread of his team’s success, other researchers across Monash University and the CSIRO approached Dr Surmiak, seeking permission to adopt his recipes and microfluidic mixers into their projects.
ANFF’s ability to immediately understand what researchers are interested in and develop streamlined relationships for the fast delivery of projects has played an important role in Dr Surmiak’s research success. ‘The ANFF-SA team are open and honest professionals who have helped our team to recognize the bottlenecks and our process limitations,’ said Dr Surmiak. ‘We were able to learn from ANFF-SA’s experience and employ those skills to further the development of our perovskite solar cells.’
The great range of tools and scientific support available through the ANFF network will hopefully help his team with future developments in reproducible, automated recipes for materials fabrication, which he hopes will lead to fully printed flexible PSCs, providing affordable, high-efficiency power conversion at scale.